In today’s world of automation and technological advancement, many options are available for streamlining your operations and improving efficiency to make your life easier.
And one area where automation can really make a difference is in packaging. Imagine saving time, reducing costs, and improving the overall quality of your packaging process. That’s where automated packaging comes in!
In this blog post, I’ll guide you through the process of transitioning to automated packaging. I’ll cover all the benefits, features, and important considerations you must remember. So whether you’re already considering automation or just curious about what it can do for your business, keep reading to learn more!
What Is Automated Packaging?
The Automated Packaging market is expected to be valued at $58,010 in 2023, which is an 8.2% CAGR compared to the market value in 2016, valued at $33,866 million. That’s a good jump!
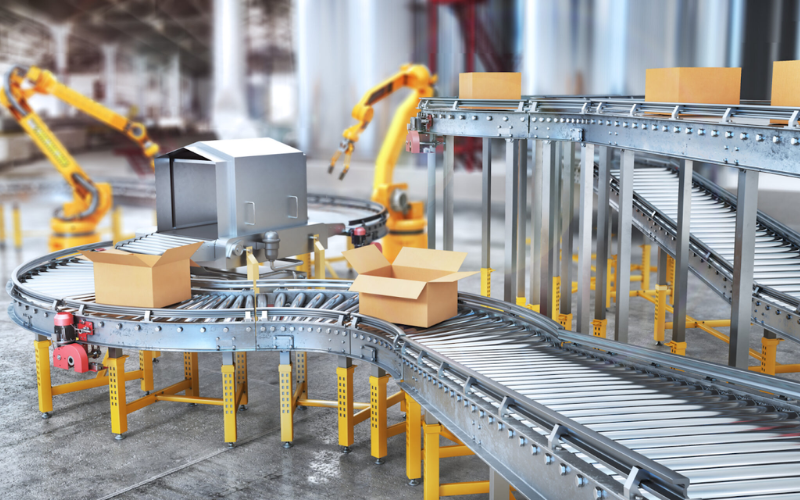
As the name suggests, automated packaging is the process where the product packaging is automated using machines, such as wrapping machines, filling stations, and more. Over the years, these machines have transformed from single machines that automate one single step of the process to all steps of product packaging, seamlessly integrating the entire process. It enables manufacturers and producers to optimize their productivity and resources by offering a constant output.
And the best part? Automated packaging systems come in all shapes and sizes, so no matter what your business needs are, there’s a system out there that can be customized to fit your exact needs. That being said, the process of automating packaging requires considerable thought from its design stage to its completion.
Types of Automated Packaging Equipment
There are several different types of automated packaging equipment available. Each one has its own set of awesome features and benefits. Some common types of packaging machines include:
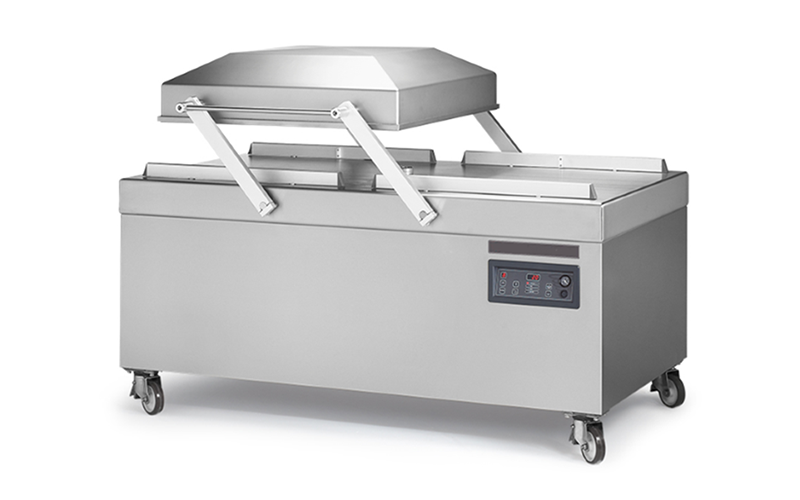
- Filling Machines or Granular Machines
These machines are used to fill products, such as liquids, powders, or granular materials, into containers.
- Sealing Machines
Sealing Machines are used to seal products in various types of packaging, such as bags, pouches, or containers.
- Wrapping Machines
Wrapping Machines are used to wrap products in films or other materials for protection or to enhance the product’s appearance.
- Labelling Machines
These machines are used to apply labels or stickers to product packaging.
- Capping Machines
Capping machines are used to apply caps or lids to containers, such as bottles or jars.
- Cartoning Machines
Cartoning Machines are used to package products in cardboard cartons, such as for food products or pharmaceuticals.
- Blister Packaging Machines
Blister Packaging Machines are used to create and fill small plastic containers with products, such as medication or small items.
- Vacuum Packaging Machines
Vacuum Packaging Machines are used to remove air from the packaging before sealing, to help preserve the freshness of food products.
These are just a few examples of the many types of packaging machines available. The specific type of machine used depends on the product being packaged and the desired packaging format.
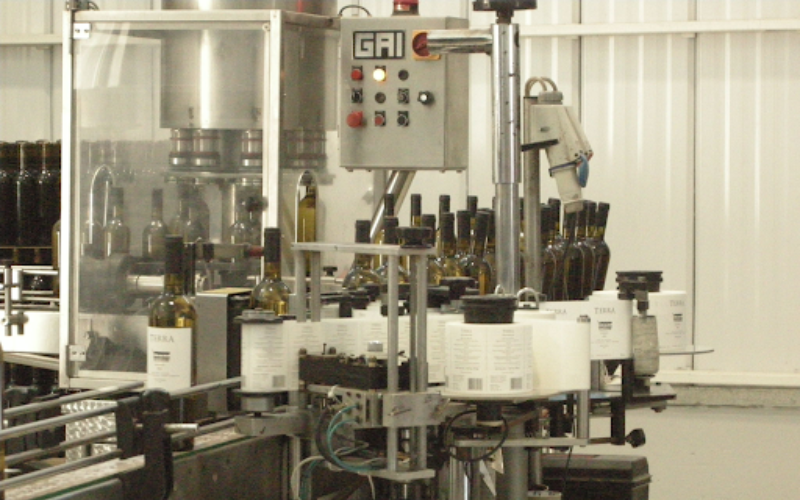
Implementation of Automated Packaging Systems
Implementing an automated packaging system requires careful planning and consideration. Here is a quick run-through of some important steps involved in the implementation process:
1. Identifying the Needs of the Business
First, you need to identify your business needs. Seeking answers to the following questions can help you make a decision:
- What kind of products do you want to package?
- What is your present production capacity?
- What is the production capacity you are aiming for?
- What kind of budget are you working with?
- Will the demand for your product increase in the future?
- Do you want to automate the entire packaging process or just one of the steps?
- What will happen if you automate packaging?
Once you have a clear idea, it’s time to choose a suitable machine for the job.
2. Choosing the Right Machine and Supplier
Choosing the right device is a critical step in the process. You’ll want to think about things like the type of product you’re packaging, your production volume, budget, employee skills, space, and more. Make sure you do your research and select a machine that meets your needs.
When it comes to choosing the right supplier, you need to count on a lot of points. The following are some of them:
- Where is the supplier based?
- How good are their machines?
- How well trained their service staff is?
- What are their reviews in the market?
- What is the availability for different parts?
Ask these questions to your suppliers. Also, see what their existing customers have to say about them.
3. Installation and Training
Once you’ve chosen your machine, it’s time to install it and set it up. Your employees will also need to be trained on how to operate and maintain the machine. So check if the supplier can help with training as well. If not, you may need to find someone who can come in and teach your employees how to use these machines.
This is a crucial step in ensuring everything runs smoothly once the system is up and running. So take it slow if needed.
4. Testing, Evaluation, and Re-evaluation
After installation and training, testing your new system is crucial. You’ll want to ensure it’s functioning correctly and meeting your business’s needs. Learn what may cause the machine to stop working or work slower than usual. Also, learn how to use it optimally.
Finally, don’t forget to re-evaluate your machine and systems every 6 months or so. It is an important step to ensure that the system works well for you over time.
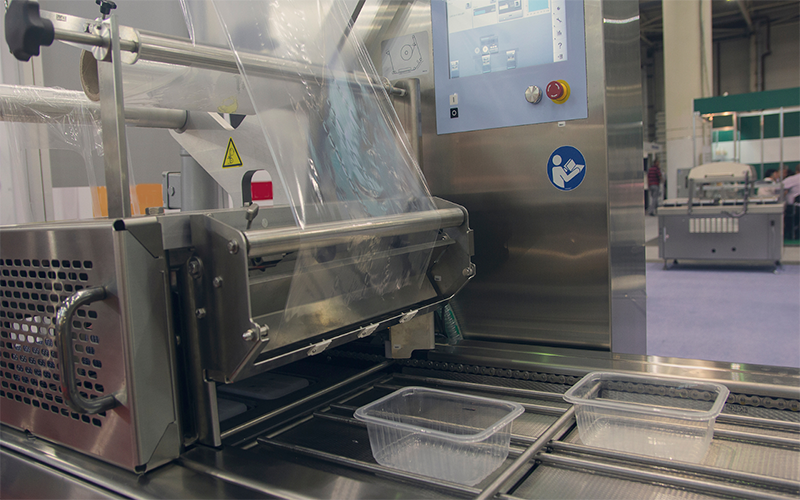
Considerations When Making the Move to Automated Packaging
If you’re considering switching to automated packaging, there are a few essential things to remember. Let’s dive in!
1. Assessing Demand
Taking a step back and assessing your production capacity is crucial. As the business market grows, so does the demand for the product. In such cases, if the production line is not optimized accordingly, it builds up immense pressure. You need to look at the bigger picture while making this decision. Is automated packaging the right choice for your business? It’s important to consider your needs and goals before taking the plunge.
2. Operation Costs
Next, you must evaluate the costs associated with automated packaging equipment. This includes upfront costs, ongoing maintenance costs, and the cost of training employees to operate the equipment. Don’t forget to factor in the space required for the equipment and any modifications that may need to be made to your facility.
3. Impact on the Workforce
Consider the type of impact it will have on manual labour. Ask yourself these questions:
- Will you need to eliminate some and hire a set of more skilled employees?
- Can you retain the current ones and train them?
- Will automated packaging eliminate some manual labour positions?
It’s important to consider the potential effects on your employees and plan accordingly.
4. Quality and Customer Service of the Equipment Supplier
Make sure you research and select the right equipment supplier. You want to choose a reputable company with quality equipment and excellent customer service. So check whether or not they have the required expertise.
Furthermore, check how long they take to resolve any issues. Longer turnaround times can affect your packaging process. This, in turn, can disrupt the supply chain process. So do your homework and make an informed decision.
5. Features
Automated packaging equipment comes with several features that can enhance the efficiency and effectiveness of your packaging process.
For example, some equipment comes with automatic product feeding systems that can improve the speed and accuracy of the packaging process. Other features may include automated sealing and cutting systems, barcode scanning, and labelling systems. When selecting automated packaging equipment, it is important to consider the features that will best suit your business’s specific needs.
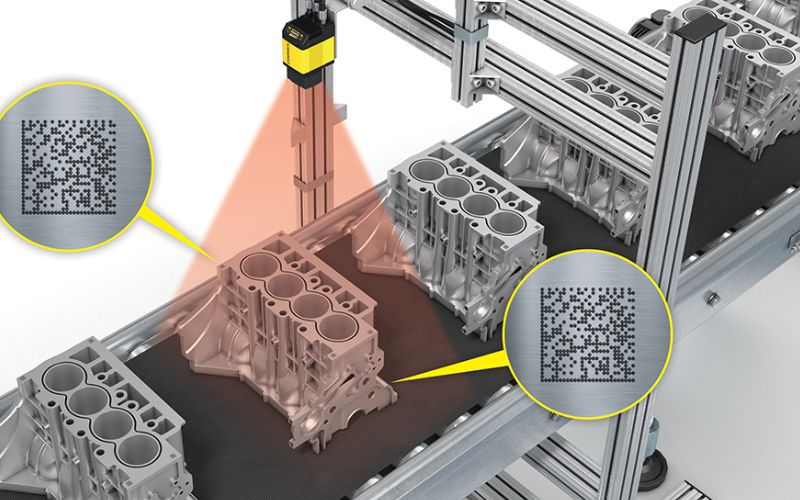
Benefits of Automated Packaging
Implementing Automated packaging is a step into the future for a business. With several benefits across multiple verticals, automated packaging streamlines the workflow while increasing the production capacity at the same time. But that’s not all. Here are some more ways in which automated packaging makes an impact on a business.
- Businesses can focus on other essential tasks by automating the process. Thus increasing productivity and efficiency.
- Automated packaging ensures higher levels of consistency and accuracy, resulting in fewer mistakes and less material going to waste. This translates to significant cost savings for businesses in the long run.
- Businesses can save on hiring and training costs by eliminating the need for additional labour.
- Automated packaging reduces the overall production cost of a product by eliminating manual labour at certain levels and optimizing the bottom line.
All in all, automated packaging is a win-win situation for businesses – it saves time, improves accuracy, and helps cut down costs.
Conclusion
After digging into the topic of automated packaging, it’s clear that businesses can reap many benefits from adopting this technology. From increased speed and efficiency to customized packaging solutions, there are plenty of reasons to consider automating your packaging process.
But before you dive headfirst into purchasing the first automated packaging system you come across, you should keep a few things in mind. Consider the type of product you’re packaging, your production volume, and your budget. With some planning and strategizing, you can set yourself up for success with an automated packaging system that meets your specific needs.
If you are looking to automate your packaging process, look no further than Accurate Meezan. Our extensive range of weighing and material handling solutions includes state-of-the-art automated packaging equipment. Contact us today to discover how our automated packaging solutions can enhance your business operations.
0 Comments